Aluminum: it’s all around us, yet how much do we really know about this remarkable metal? From soda cans to airplanes, aluminum plays a crucial role in our daily lives. But what makes aluminum so special? In this comprehensive guide, we’ll answer 130 common questions about aluminum, shedding light on its properties, applications, manufacturing processes, and sustainability practices.
Understanding Aluminum:
Let’s start with the basics. What is aluminum, and why is it so widely used? Aluminum is a lightweight, silvery-white metal known for its exceptional strength-to-weight ratio and corrosion resistance. These properties make it ideal for a wide range of applications across various industries, including aerospace, automotive, construction, and packaging.
Properties and Characteristics:
What gives aluminum its unique properties? Aluminum owes its remarkable characteristics to its atomic structure and chemical properties. With a low density and high thermal conductivity, aluminum is prized for its lightweight yet durable nature. Additionally, its ability to resist corrosion ensures longevity in harsh environments.
Is aluminum an environmentally friendly material? Despite its widespread use, aluminum boasts impressive sustainability credentials. It is highly recyclable, with recycled aluminum requiring significantly less energy to produce than virgin aluminum. Moreover, aluminum’s light weight helps reduce fuel consumption in transportation, further mitigating its environmental impact.
Applications Across Industries:
Where can we find aluminum in our everyday lives? From the fuselage of airplanes to the frames of skyscrapers, aluminum’s versatility knows no bounds. In the automotive industry, aluminum is used to reduce vehicle weight and improve fuel efficiency. In construction, it provides strength and durability without adding unnecessary bulk. And in packaging, aluminum foil keeps our food fresh and our drinks cold. Despite its lightweight, aluminum boasts excellent conductivity properties, allowing for efficient transmission of electrical power over long distances. Aluminum conductors exhibit comparable electrical conductivity to copper, making them an attractive choice for high-voltage transmission lines .
Manufacturing Processes:
How is aluminum produced? The journey from bauxite ore to finished aluminum products involves several intricate steps. These include mining and refining bauxite, smelting alumina to produce aluminum metal, and shaping the metal into various forms through casting, extrusion, and rolling processes.
In conclusion, aluminum is a multifaceted metal with a myriad of applications and benefits. From its remarkable properties to its diverse range of uses across industries, aluminum continues to shape our world in profound ways. By understanding the answers to 130 common questions about aluminum, we gain a deeper appreciation for this essential material and its role in our lives.
130 Common Questions & Answers About Aluminum: A Comprehensive Guide:
Aluminum rods are used in various applications due to their strength-to-weight ratio, corrosion resistance, and recyclability. Common uses include:
Overhead Transmission Lines: Aluminum wire rods, renowned for their strength and flexibility, are extensively utilized in the construction of overhead transmission lines, facilitating efficient electricity distribution over long distances. the conductors such as AAC, AAAC, and ABC, which are widely used in the electrical industry.
Fasteners: Aluminum’s favorable mechanical properties make it an ideal choice for manufacturing fasteners such as nuts, bolts, and screws, ensuring robust connections in electrical infrastructure.
Transformers: Aluminum’s lightweight nature makes it a preferred material for manufacturing transformer windings, enabling the construction of efficient transformers for voltage regulation in power distribution networks.
Underground Cables: Aluminum wire rods are employed in the production of underground cables, catering to urban infrastructural requirements with their durability and corrosion resistance.
Deoxidation: Aluminum Rod 12 is utilized in the steel industry for deoxidation purposes. Deoxidation is a critical step in the steelmaking process aimed at removing oxygen from the molten steel. The presence of oxygen in steel can significantly alter its mechanical properties, rendering it brittle and less flexible. Aluminum serves as one of the most common deoxidizers for steel. With its high affinity for oxygen, aluminum effectively reacts with the oxygen present in the molten steel, forming aluminum oxide (Al2O3). While this aluminum oxide remains as an impurity in the steel, it does not have detrimental effects akin to free oxygen.
The strength of an aluminum rod depends on the alloy and temper used. While common grades like 6061 and 7075 offer good strength for their weight, they are not necessarily stronger than steel overall. Aluminum rods will bend under sufficient force.
Yes, aluminum rods can be strong relative to their weight, making them suitable for applications where lightness is crucial. However, they might not be the strongest option in all situations.
The choice between aluminum and steel depends on specific application requirements. Aluminum offers weight savings, while steel provides higher overall strength. The best option varies based on the application’s needs.
Yes, aluminum rods can be used alongside steel. However, precautions should be taken to prevent galvanic corrosion, a type of corrosion that occurs when dissimilar metals are in contact with each other in the presence of an electrolyte like moisture.
No, aluminum rods themselves do not rust. They develop a thin oxide layer that protects the metal from further oxidation, making aluminum suitable for outdoor applications.
While no metal is completely immune to corrosion, some metals like gold and platinum are highly resistant to rust.
Aluminum does not significantly react with water at room temperature due to the protective oxide layer. However, under specific conditions like high temperatures or exposure to strong acids/bases, it can react.
While aluminum resists rust due to its oxide layer, it can corrode under specific conditions such as saltwater exposure or prolonged contact with other metals.
You can put aluminum on steel, but precautions are needed to prevent galvanic corrosion. Dissimilar metal contact can accelerate corrosion. Specialized fasteners or isolation techniques can mitigate this.
Yes, aluminum rods can be bent, especially compared to steel. The ease of bending depends on the thickness, temper, and alloy of the rod.
Aluminum can be welded but requires special techniques due to its high thermal conductivity. Regular welding methods may result in burning through the metal.
Titanium rods are stronger than aluminum but more expensive. They’re ideal for applications requiring high strength-to-weight ratio and corrosion resistance, like aerospace.
Aluminum rods come in various grades (alloys) with different properties, such as 6061 (good strength and workability), 7075 (high strength), and 5052 (excellent corrosion resistance).
The strongest rod material varies depending on specific requirements. Steel offers high overall strength, while titanium provides excellent strength-to-weight ratio. Advanced composites may offer even greater strength.
No, steel generally offers higher overall strength than aluminum. However, aluminum can provide good strength for its weight, making it valuable in weight-critical applications.
Aluminum rods are not necessarily weak but offer lower overall strength compared to steel. However, they provide weight savings, making them suitable for certain applications.
The strongest metal rod depends on specific requirements such as tensile strength, compressive strength, or strength-to-weight ratio.
Weakness depends on the type of stress applied. Alkali metals like lithium are soft, while lightweight metals like magnesium may be weak in tension.
High-strength steel alloys and advanced composites may exceed titanium’s strength in certain aspects.
No, aluminum is not bulletproof due to its low density and hardness. It can be used in non-critical components in firearms.
Pure aluminum is relatively soft and weak compared to its alloys. Alloying significantly improves its strength and other properties.
Pure aluminum has low strength and a lower melting point compared to alloys.
Yes, aluminum rods can bend under sufficient force, depending on factors like thickness, alloy, and temper.
No, aluminum is not as strong as titanium overall.
Aluminum rods come in various thicknesses depending on the application’s requirements.
7075 aluminum is generally stronger than 6061 but may be less workable.
The strength of 5mm aluminum depends on the specific alloy, but it wouldn’t be suitable for extremely high-stress applications.
No, 7075 T6 aluminum is not generally stronger than steel.
Yes, but precautions should be taken to prevent galvanic corrosion.
Aluminum, especially certain alloys, can be more prone to cracking under certain conditions.
Yes, but precautions should be taken to prevent galvanic corrosion.
Aluminum, especially certain alloys, can be more prone to cracking under certain conditions.
Yes, but it requires special techniques and equipment due to aluminum’s high thermal conductivity
Aluminum wire rods typically range in diameter from 9.5 mm to 25 mm, with variations depending on specific industry requirements.
Yes, titanium rods offer high strength and low weight.
Not necessarily; strength depends on various factors like material properties and design.
Common alloying elements added to aluminum wire rods include copper, magnesium, silicon, and zinc, which improve strength, corrosion resistance, and conductivity.
Titanium is generally stronger than aluminum.
Depends on the type of strength needed.
Vibranium is a fictional metal from Marvel Comics and does not exist in reality. Vibranium is a fictional metal originating from Marvel Comics. It possesses various extraordinary properties, including superhuman strength and the ability to absorb vibrations. Since it’s fictional, there’s no real-world equivalent for vibranium.
Yes, the military uses aluminum in various applications due to its lightweight properties.
Aluminum can be used for certain non-critical components in firearms due to its lightweight nature.
Yes, pure aluminum can be produced, but it’s not commonly used due to its low strength and mechanical properties.
Pure aluminum isn’t commonly used due to its low strength and melting point, making it unsuitable for many applications.
Aluminum is generally considered safe, but prolonged exposure to high levels may have health effects.
Expensive rods may offer better materials and performance, but the difference depends on the application.
Disadvantages include high cost and difficulty in machining.
Titanium generally has better corrosion resistance and durability.
Yes, aluminum can be welded using appropriate techniques
Aluminum welds can be weaker due to factors like porosity and lack of fusion.
Brazing aluminum to steel can be challenging due to differences in melting temperatures.
The weakest metal depends on various factors such as alloy composition and application.
Depends on the type of strength being measured.
Materials like tungsten and certain ceramics may be stronger than titanium.
No, aluminum is not typically used as a bulletproof material.
Pure aluminum is relatively soft and weak compared to its alloys.
Low strength and a lower melting point.
Aluminum is relatively inexpensive compared to some other metals.
Aluminum is not inherently “poor” but has lower tensile strength compared to some other metals.
Pure aluminum lacks strength and mechanical properties needed for most applications.
Lead and tin are relatively soft and weak compared to stronger metals like steel.
The top five hardest metals based on their hardness are tungsten, chromium, titanium, rhenium, and osmium. Tungsten stands out with the highest tensile strength and a very high melting point, making it incredibly hard and durable. Chromium is also extremely hard and well-known for its excellent corrosion resistance. Titanium combines high strength with a low weight and impressive corrosion resistance. Rhenium is notable for retaining its hardness at high temperatures and has one of the highest melting points among metals. Osmium, although less commonly discussed, is one of the densest and hardest metals, providing excellent wear resistance. These metals are widely used in industries requiring materials that can withstand extreme conditions and wear.
Depends on various factors such as alloy composition and application.
Strong acids, alkalis, and certain metal chlorides at elevated temperatures can attack titanium.
No, titanium is known for its high strength-to-weight ratio.
Titanium is generally stronger than aluminum.
Vibranium is fictional and not a real-world material
Steel is generally stronger and more rigid than aluminum.
Yes, the military uses aluminum in various applications due to its lightweight properties.
Aluminum can be used for certain non-critical components in firearms due to its lightweight nature.
Yes, pure aluminum can be produced, but it’s not commonly used due to its low strength and mechanical properties.
Pure aluminum isn’t commonly used due to its low strength and melting point, making it unsuitable for many applications.
Aluminum is generally considered safe, but prolonged exposure to high levels may have health effects.
Expensive rods may offer better materials and performance, but the difference depends on the application.
Disadvantages include high cost and difficulty in machining.
Titanium generally has better corrosion resistance and durability.
Yes, aluminum can be welded using appropriate techniques.
Aluminum welds can be weaker due to factors like porosity and lack of fusion.
Brazing aluminum to steel can be challenging due to differences in melting temperatures.
The weakest metal depends on various factors such as alloy composition and application.
Depends on the type of strength being measured.
Materials like tungsten and certain ceramics may be stronger than titanium.
No, aluminum is not typically used as a bulletproof material.
Pure aluminum is relatively soft and weak compared to its alloys.
Low strength and a lower melting point.
Aluminum is relatively inexpensive compared to some other metals.
Aluminum is not inherently “poor” but has lower tensile strength compared to some other metals.
Pure aluminum lacks strength and mechanical properties needed for most applications.
Lead and tin are relatively soft and weak compared to stronger metals like steel.
The top five most expensive metals are rhodium, platinum, gold, palladium, and iridium. Rhodium is the most expensive metal due to its rarity and use in automotive catalytic converters, which help reduce emissions. Platinum, another precious metal, is highly valued for its applications in jewelry, automotive catalysts, and various industrial processes. Gold, long considered a symbol of wealth, is used extensively in jewelry, electronics, and as a financial asset. Palladium, similar to platinum, is used in catalytic converters and electronics, and its price has surged due to supply constraints. Iridium, one of the rarest metals, is highly resistant to corrosion and is used in specialized industrial equipment and medical devices. These metals are not only rare but also have significant industrial and commercial applications, driving their high value.
The five cheapest metals, often characterized by their abundance and low cost, are iron, aluminum, zinc, lead, and copper. Iron, the most widely used metal, is inexpensive due to its plentiful supply and extensive use in construction, manufacturing, and automotive industries. Aluminum, known for its lightweight and corrosion-resistant properties, is also relatively cheap and widely used in packaging, transportation, and construction. Zinc, often used for galvanizing steel to prevent rust, is affordable and widely available. Lead, though less commonly used today due to health concerns, remains inexpensive and is used in batteries and radiation shielding. Copper, while more expensive than the other four, is still considered cheap relative to precious metals and is essential for electrical wiring, plumbing, and telecommunications. These metals are integral to numerous industries due to their affordability and versatile properties.
Aluminum wire rods for electrical applications typically have a conductivity ranging from 61.0 to 64.9% International Annealed Copper Standard (IACS).
Aluminum wire rods are typically produced through continuous casting and rolling processes, where molten aluminum is cast into cylindrical billets and then hot rolled into wire rod coils of various diameters.
The mechanical properties of aluminum wire rods are primarily influenced by factors such as alloy composition, heat treatment, and processing parameters during manufacturing.
Aluminum wire rods find applications in automotive components such as engine blocks, pistons, wheels, and structural parts due to their lightweight, high strength, and corrosion resistance properties
Aluminum wire rods generally have a lower cost compared to copper wire rods, making them a preferred choice for various industrial and electrical applications where cost-effectiveness is a priority.
Aluminum wire rods offer environmental benefits such as reduced energy consumption during production, lower greenhouse gas emissions, and ease of recyclability, contributing to sustainable manufacturing practices.
Common surface finishes for aluminum wire rods include mill finish, anodized finish, polished finish, and coated finish, with each offering specific aesthetic and functional properties for different applications.
International standards organizations such as ASTM International and ISO provide guidelines for the chemical composition, mechanical properties, dimensions, and tolerances of aluminum wire rods to ensure quality and compatibility across global markets.
Aluminum wire rods are commonly packaged in coils, spools, or bundles, with protective coatings or wrapping to prevent damage from moisture and handling during transportation and storage.
Aluminum wire rods offer advantages such as lighter weight, lower sag, higher conductivity per unit weight, and reduced cost compared to traditional materials like copper, making them ideal for long-span transmission lines.
The mechanical strength of aluminum wire rods can vary significantly depending on the alloy composition, with alloys containing elements like magnesium and zinc exhibiting higher strength compared to pure aluminum or low-alloy grades.
The conductivity of aluminum wire rods is primarily influenced by factors such as alloy composition, impurities, grain structure, and processing conditions during manufacturing.
Surface quality and integrity of aluminum wire rods are ensured through processes such as surface inspection, cleaning, descaling, and protective coatings applied during manufacturing to meet industry standards and customer requirements.
Aluminum wire rods used in construction typically exhibit tensile strength ranging from 120 to 190 MPa and elongation values of 10% to 25%, depending on the specific alloy and heat treatment.
Industry standards such as ASTM B233/B233M and EN 1715-2 classify aluminum wire rods into different grades based on their alloy composition, mechanical properties, and intended applications.
Common testing methods for aluminum wire rods include tensile testing, hardness testing, conductivity testing, metallographic analysis, ultrasonic inspection, and surface quality assessment to ensure compliance with industry standards and customer specifications.
Alloying elements like copper and magnesium enhance the corrosion resistance of aluminum wire rods by forming protective oxide layers on the surface, reducing susceptibility to corrosion in various environments, including marine and industrial atmospheres.
Aluminum wire rods produced through direct chill casting have a coarser grain structure and lower surface quality compared to those produced through continuous casting processes, which offer finer grain structure, better surface finish, and tighter dimensional tolerances.
Annealing processes can enhance the ductility and formability of aluminum wire rods by relieving internal stresses, refining the grain structure, and improving uniformity, resulting in improved mechanical properties and machinability.
Aluminum wire rods find applications in aerospace components such as fuselage structures, wing panels, landing gear, and interior fittings due to their lightweight, high strength-to-weight ratio, and corrosion resistance properties.
Industry standards such as ASTM B316/B316M and EN 1715-1 specify dimensional tolerances for diameter, ovality, straightness, and coil weight of aluminum wire rods to ensure consistency and compatibility in manufacturing and assembly processes
Surface treatment methods such as anodizing, chromating, painting, and powder coating are commonly used to provide corrosion protection and enhance the aesthetic appearance of aluminum wire rods for various outdoor and marine applications.
The recycling process of aluminum wire rods requires significantly less energy compared to primary production, reduces greenhouse gas emissions, conserves natural resources, and minimizes waste generation, making it an environmentally sustainable practice.
Common surface defects in aluminum wire rods include surface cracks, pits, scratches, roll marks, oxide inclusions, and surface contamination, which can affect product quality and performance if not properly controlled and mitigated.
Casting and rolling parameters such as casting temperature, cooling rate, rolling speed, and reduction ratio influence the microstructure, grain size, texture, and mechanical properties of aluminum wire rods, requiring optimization for desired product characteristics.
Commercially produced aluminum wire rods may contain impurities and trace elements such as iron, silicon, manganese, titanium, and chromium, which can affect alloy properties and processing behavior, necessitating control and analysis during production.
Intermetallic phases in aluminum wire rods can affect mechanical properties, such as strength, ductility, and toughness, as well as machinability, depending on their morphology, distribution, and chemical composition, requiring consideration in alloy design and processing.
Surface cleaning and preparation methods for coating aluminum wire rods include mechanical cleaning (brushing, grinding), chemical cleaning (pickling, degreasing), and surface treatment (conversion coating, phosphating) to remove contaminants and promote adhesion and durability of protective coatings.
Elka Mehr Kimiya specializes in manufacturing aluminum rods, alloys, conductors, ingots, and wire.
Elka Mehr Kimiya’s aluminum rods stand out due to their high quality, durability, and adherence to stringent quality control measures with competitive price
Elka Mehr Kimiya ensures the reliability of its aluminum rods through advanced manufacturing processes and ISO-certified quality management systems.
Elka Mehr Kimiya utilizes advanced technology in its manufacturing processes to produce aluminum rods with precise dimensions and mechanical properties.
Elka Mehr Kimiya employs advanced production techniques and optimized operations to offer aluminum rods at competitive prices without compromising on quality.
Elka Mehr Kimiya is certified with ISO 9001:2015, ISO 14001:2015, ISO 10004:2018, and adheres to Doc International’s quality standards.
Elka Mehr Kimiya offers aluminum rod products such as ALUMINUM ROD 9.5 ALLOY, ALUMINUM ROD EC9.5, and ALUMINUM ROD 12, each tailored to specific industry needs.
Elka Mehr Kimiya’s team of experts provides professional and personalized service, offering technical support and guidance to ensure customers make informed decisions.
Industries ranging from power transmission to steel manufacturing benefit from the reliability and performance of Elka Mehr Kimiya’s aluminum rods.
Elka Mehr Kimiya acts as a partner in success, offering comprehensive customer support from product selection to after-sales assistance, backed by unmatched expertise.
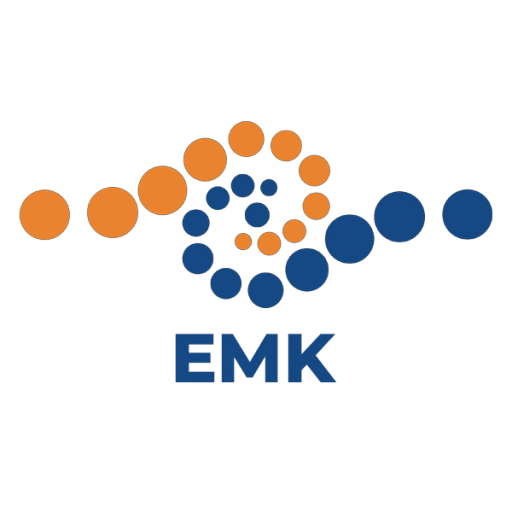
Excellence in Aluminum Rods: Discover the Elka Mehr Kimiya
Elka Mehr Kimiya stands out as the premier choice for aluminum rods, offering a myriad of compelling reasons to choose our products. With a relentless focus on quality and durability, our aluminum rods are meticulously crafted from the finest materials and subjected to rigorous quality control checks, ensuring unparalleled reliability across various applications. Backed by ISO-certified manufacturing processes and compliance with Doc International standards, our products consistently deliver exceptional performance that exceeds industry benchmarks.
Our commitment to advanced manufacturing processes ensures that our aluminum rods boast precise dimensions and excellent mechanical properties, guaranteeing consistent performance in any application. Despite our unwavering dedication to quality, we remain cognizant of the importance of cost-efficiency. Through optimized operations and advanced production techniques, we offer our aluminum rods at competitive prices without compromising on quality, providing our customers with unmatched value for their investment.
At Elka Mehr Kimiya, our comprehensive product range includes aluminum rods tailored to specific industry requirements and applications, such as overhead power transmission lines, electrical conductors, and steel manufacturing processes. With our professional and personalized service, our team of experienced professionals is committed to providing exceptional customer support, assisting with inquiries, and ensuring a seamless buying experience.
Our High Quality aluminum rods with competitive Prices , including ALUMINUM ROD 9.5 ALLOY, ALUMINUM ROD EC9.5, and ALUMINUM ROD 12, exemplify our dedication to excellence and innovation. From technical guidance to after-sales support, Elka Mehr Kimiya goes above and beyond to serve as your trusted partner in success. Choose Elka Mehr Kimiya for unmatched expertise, exceptional products, and unparalleled customer support in the world of aluminum rods.
Contact us today to discuss your specific production requirements and learn more about how Elka Mehr Kimiya’s Aluminum Rods can elevate your steelmaking process.
Whatsapp Number:
+98-902-8000013
Sale Department Contact Number:
+98(41)36589245
No comment